What is needed to design and quote a shell and tube heat exchanger?
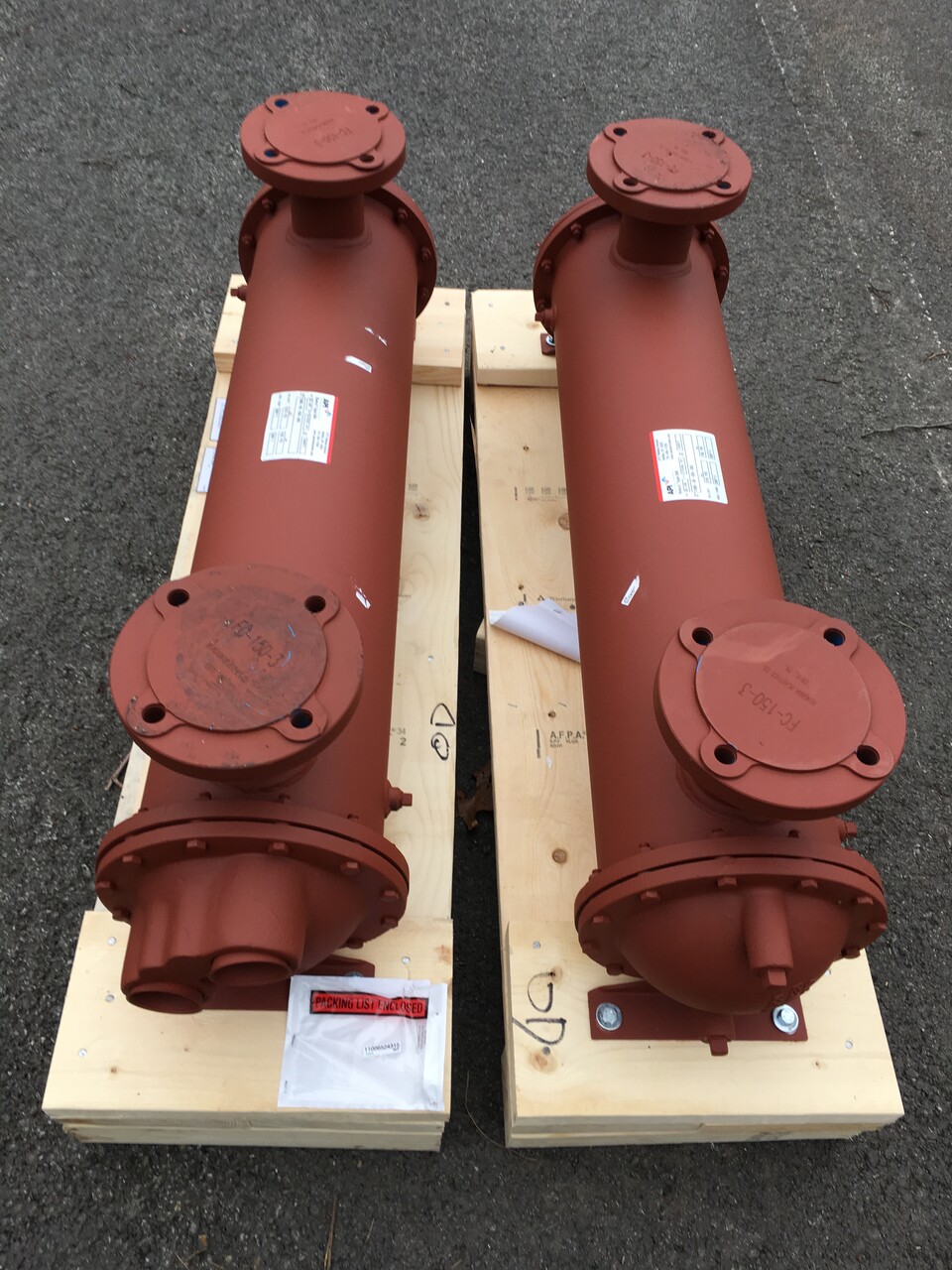
When the design engineers at Thermal Products have a request from a customer to design a shell and tube exchanger, we will consider many factors, including:
- What codes and/or standards will guide the design: ASME Boiler and Pressure Vessel Code, TEMA standards, and API (American Petroleum Institute), PED (Pressure Equipment Directive – Europe), CRN (Canadian Registration Number). All guide our engineers to offer the most optimally designed shell and tube heat exchanger while ensuring safety, reliability, and efficiency.
- Process requirements: These include process and utility fluid or gas types, flow rates, process side inlet temperature, process side outlet temperature, utility side inlet temperature, and operating pressure.
- Configurations: Here our design engineers will take into account our customer needs and requests for how their shell and tube heat exchanger will look.
- What orientation do you need your shell and tube heat exchanger? Horizontal, vertical or sloped for drainability?
- Do you need all tube side connections on one side?
- Where do you want your shell side connections oriented on the shell? We can orient them 360 degrees around the shell in most cases to better suit your process needs.
- Are NPT or Flanged connection needed?
- Design elements: Baffle cut, spacing, and orientation, as well as tube-side channel and nozzle design, can all affect performance with regards to pressure drop, velocity, heat transfer rate and final footprint size.
- Construction materials: Shell materials can include carbon steel, stainless steel, or alloys, while tubes can be copper, aluminum, stainless steel, or other alloys.
- Physical space: The available floor space for installation is also a consideration.
Please look for Thermal Products Shell and Tube Heat Exchanger RFQ form or click here.
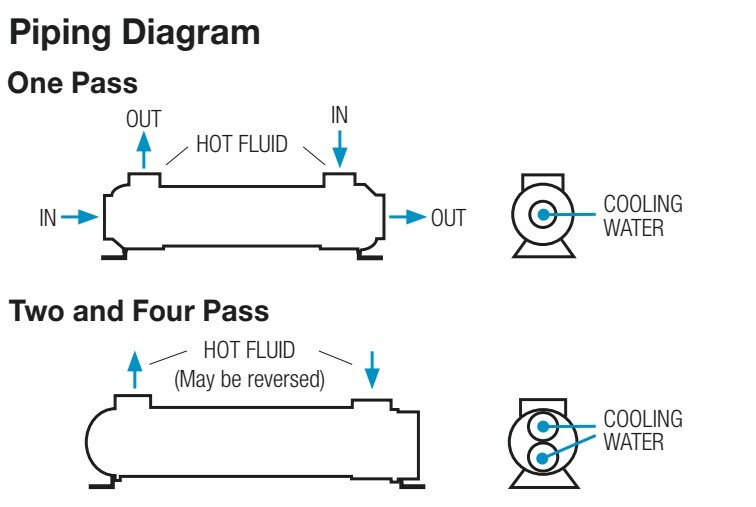
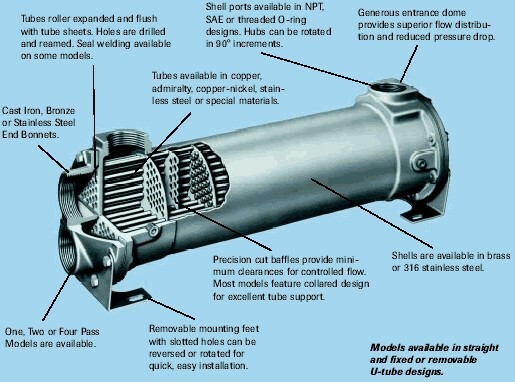
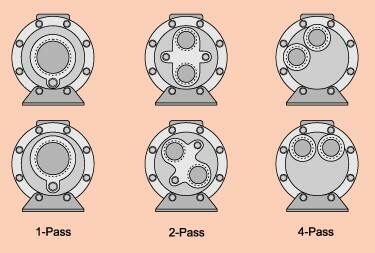