Heat Transfer Performance
The unique designs of our thermal plates produce high turbidity thus offering high heat transfer coefficients for a given application, resulting in lower heat transfer surface area and lower capital cost.
Compact Design
Plate heat exchangers contain large heat exchanging surfaces in a very compact, space-saving frame. This results in a much smaller space requirement and lower weight and cost.
Versatility
Plates are formed in a wide variety of patterns and materials to meet your heat transfer needs and process fluids. Stainless steel, Monel, Hastelloy, titanium and other higher alloys plate offerings.
Peak Efficiency
With high heat transfer coefficients and a true counter-current flow path, the Schmidt Bretten plate heat exchangers perform well with tight approach temperatures, cooling hot fluids to within one degree of the cold fluid making heat recovery in excess of 96% technically and economically possible.
Minimal Fouling
Fouling of the heat transfer surfaces of the plate heat exchanger is extraordinarily low. The high induced turbulence and polished heat transfer surface, yields a self-cleaning effect, which minimizes fouling.
Easy Maintenance
Units can be cleaned without dismantling by clean-in-place (CIP) systems, by reverse flow cleaning or by addition of suitable cleaning fluids. However, if mechanical cleaning is needed, the Plate removal is easily accomplished by releasing the tightening bolts that compress all of the heat transfer plates.
Lower Liquid Volume
Since the gap between plates is small, a plate heat exchanger contains only low quantities of process fluids, reducing cost due to lower volume requirements.
Expandable
Plate arrangement can be changed and plates can be added or removed. It is possible to install several sections in one frame and permit several process steps in a single unit.
Reliability
The unique design of our plates allows for optimum alignment during assembly for greatest sealing capabilities
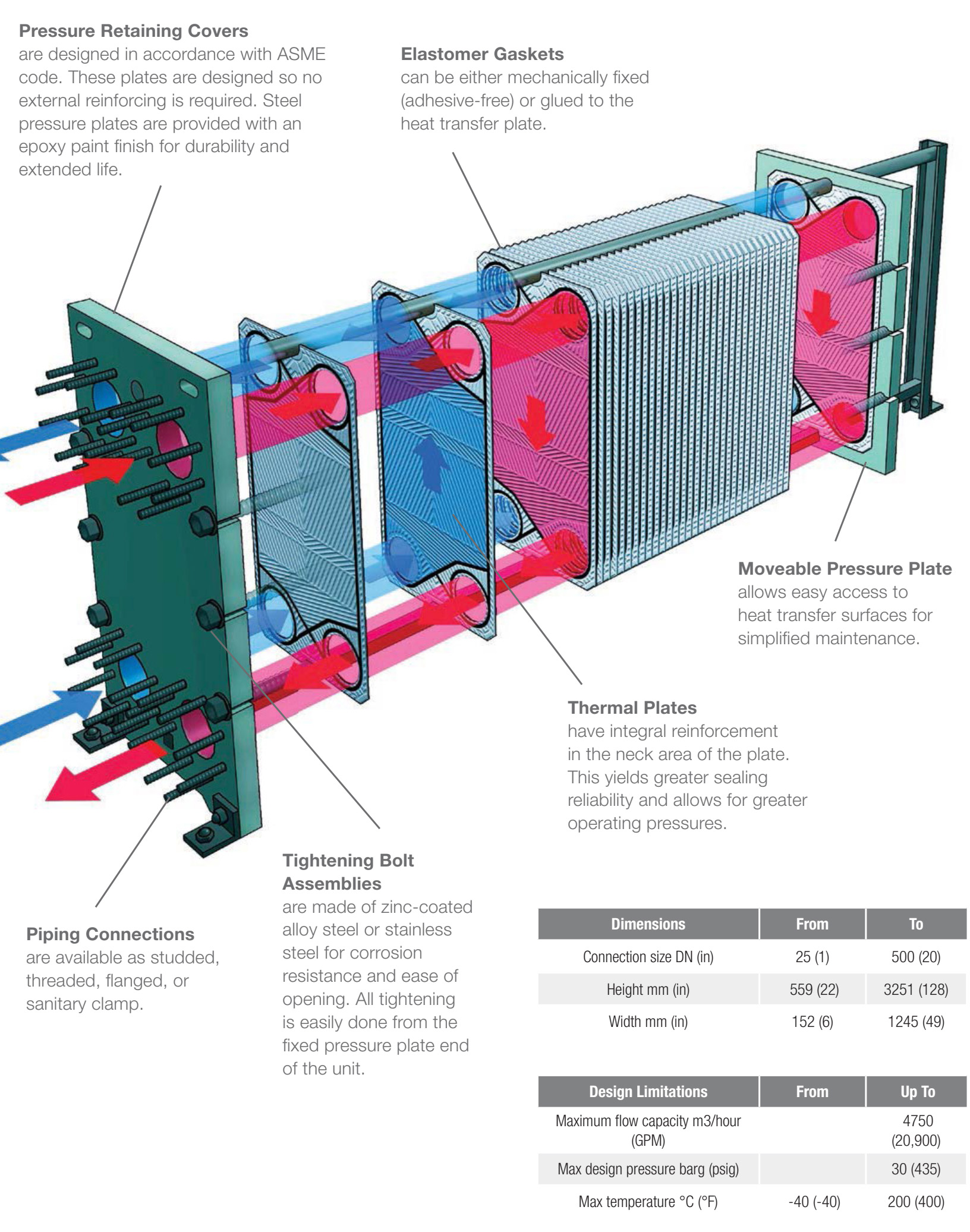